Compliance
The Dincel product is at the forefront of innovative construction by focusing on rigorous testing to meet or exceed industry standards.
Since the product was developed, Dincel engineers have continued to work closely with organisations such as the CSIRO, The University of New South Wales (UNSW), The University of Technology Sydney (UTS) and other industry recognised authorities for the testing and certification of Dincel products in relation to fire ratings, combustibility, waterproofing, earthquakes, acoustics, toxicity and VOC testing. Dincel products are BEP (Best Environmental Practice) certified.
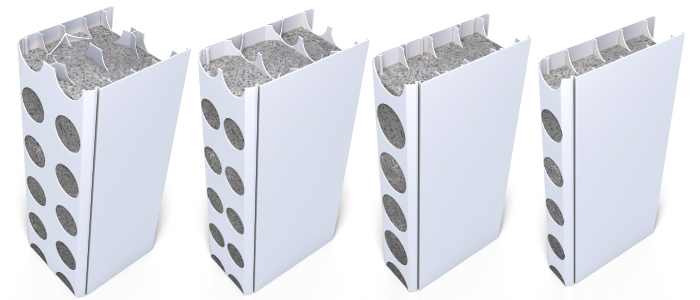
Civil & Transport Authorities
A Dincel wall, when installed in accordance with the relevant specifications and Dincel construction manual, complies with the requirements of transport infrastructure and civil authorities by offering the following:
As Dincel is purely a formwork material, the concrete and steel reinforcement inside can be designed, ordered and placed to comply with the relevant transport concrete specifications and requirements (such as RMS B80, Vic Roads 610 and QLD Transport and Main Roads MRTS70). Alternatively, if desired Dincel 275 can be designed as a composite walling system in order to substantially reduce or even eliminate steel reinforcement within walls.
For detailed information on the above, please download the following information sheet:
Fire Compliant
Dincel has undergone extensive large-scale fire testing to demonstrate safety in a variety of scenarios. The tests and assessments were performed by reputable NATA accredited authorities such as CSIRO and Warringtonfire.
The Dincel formwork material is comprised of certain additives which enhances fire performance. In the event of a fire, the material safely chars and intumesces (it does not form molten droplets or spread fire). The solid concrete within provides the necessary fire rating.
The following tests and assessments have been carried out:
AS ISO 9705 Room Test – Group 1 rating was achieved which is the best/highest classification possible. In addition, the smoke growth rate (SMOGRA) was 7 times under the limit specified in the National Construction Code. This indicates the walls suitability for confined applications such as tunnels or service shafts.
Watch AS ISO 9705 video of Dincel test resultsAS 5113/BS 8414 Façade Test – After positive test results, the system has been certified by Consulting Fire Engineers to be suitable for external façade walls which are required to be non-combustible. This indicates the walls suitability for external applications such as retaining walls.
Watch AS 5113/BS 8414 video of Dincel test resultsAS 1530.4 Fire Resistance Level (FRL) – Through multiple fire resistance tests, testing authorities CSIRO and Warringtonfire have confirmed that the polymer webs do not melt away or negatively affect the concrete wall’s performance for FRL.
It is important to note that the FRL of a Dincel wall (or any other structural wall) for a specific project requires to be calculated and provided by the project’s structural engineer to AS 3600 or other relevant concrete codes, just like for a conventional concrete wall (keeping in mind that Dincel is simply formwork for a concrete wall). The engineer must take into account project specific variables such as wall height and wall loading.
In accordance with AS 3600, Dincel can achieve up to the following FRLs:
Dincel Profile | Maximum FRL Achievable |
110mm | 90/90/90 |
155mm | 180/180/180 |
200mm | 240/240/240 |
275mm | 240/240/240 |
In addition, joint and penetration specific tests have been carried out. It has been established that there is no requirement to remove the Dincel skin underneath Hilti fire rated caulking and fire collars/penetration products.
Watch AS 1530.4 Joint Specific test results Watch AS 1530.4 Penetration Specific test resultsBushfire Attack Level (BAL) - Dincel was assessed by CSIRO and confirmed as suitable for use in bushfire conditions of up to Flame Zone (FZ), which is the most severe rating.
Non-Toxic Fumes - The Dincel polymer is manufactured without the use of heavy metal stabilisers or plasticisers. Dincel has been tested in accordance with BS 6853:1999 where it was found that the fumes generated by the burning test was well under international toxicity thresholds/limits.
Earthquake Tested
Dincel Structural Walling has been put through an extensive testing and assessment regime with The University of Technology Sydney (UTS) to determine the adequacy of the system in seismic regions. The tests include:
- Shake table simulations
- In-plane horizontal shear push over tests
The test results and accompanying analysis confirms the suitability of Dincel system to resist large lateral forces and resulting displacement caused by major ground motions measuring up to 9.0 on the Richter scale. The permanent polymer shell achieves this by working in conjunction with concrete and steel reinforcement to provide ductile composite action to the wall.
View supporting documentationStructural
Dincel structural walling is a permanent formwork system which when filled with concrete will result in a structurally sound concrete wall. The concrete and steel reinforcement inside can be designed by an engineer to AS 3600, Eurocode or other relevant design codes. For design purposes, the presence of the polymer formwork is removed and the engineer designs with the remaining effective concrete thickness. This is confirmed by certification from The University of New South Wales (UNSW) and The University of Technology Sydney (UTS). Therefore, a structural engineer can design Dincel walls to meet project specific requirements in the same manner as a conventional concrete wall. Engineers are encouraged to download our structural engineering manual for further information.
Alternatively, following testing by UTS in accordance with AS3600:2018 Appendix B, it has been verified that Dincel 275 with its unique ring webbing provides significant benefits against a range of structural actions. If desired, Dincel 275 can be designed as a composite walling system in order to substantially reduce or even eliminate steel reinforcement within Dincel 275 walls.
View supporting documentationVOC Tested
Dincel permanent formwork is classed as a low volatile organic compound (VOC) emitting product in accordance with ASTM D5116-97. Test results demonstrated that VOC emissions were less than the recognised Green Star threshold making it a proven choice for sustainable construction.
Dincel Polymer Formwork | VOC (mg/m²/hr) |
Newly Manufactured (24 hours) | 0.02 (well below Green Star limit of 0.5) |
Aged (ca. 30 days) | 0.01 (below detection limit, and well below Green Star limit of 0.5) |
Waterproof
Raw Dincel panels along with snap-joints, when filled with concrete are certified as waterproof for up to 6m head of pressure without the need for waterproofing membranes. The following tests were undertaken by CSIRO to confirm this:
ASTM E514 - 03 | Pass |
AS/NZS 2904:1995 | Pass |
ASTM E 96/M | Water vapour transmission was found to be 180 times better than the requirement for a waterproof membrane |
Best Environmental Practice PVC
Dincel has been awarded the Best Environmental Practice (BEP) Approval Mark after meeting the strict Green Building Council Best Practice Guidelines for PVC. Dincel was reviewed against the following requirements:
- Manufacture of PVC Resin
- Manufacture and end of life management of PVC products
- Use of PVC recyclate in PVC products
The Dincel polymer PVC is heavy metal stabiliser and plasticiser free. Due to this it is a certified non-toxic product and contains a VOC significantly below the green star threshold. Additionally, due to Dincel’s innovative design the wall can be designed with less cement content and steel reinforcement than a conventional concrete wall, which reduces the total embodied energy and allows for more efficient end of life recycling.
View supporting documentationAcoustic Tested
Dincel has been tested at CSIRO within their reverberation chambers. The acoustic performance, similar to a concrete wall, can be utilised for applications such as sound walls.
View supporting documentation